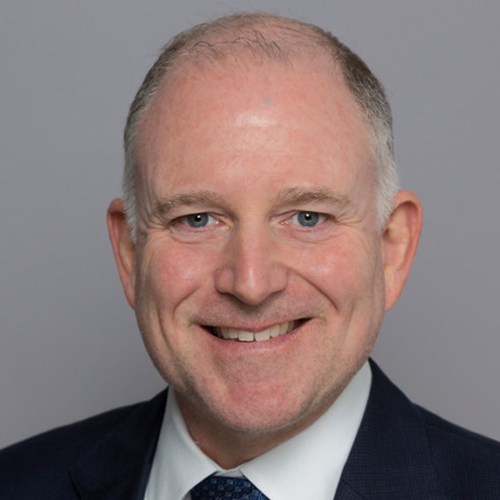
By Brooks McDaniel, Senior Vice President of Building Repositioning, STO Building Group
In the wake of the pandemic, we’ve seen a fundamental shift in how cities use space. Commercial tenants are prioritizing quality over quantity, leaving older office buildings underoccupied and underutilized. At the same time, an increase in healthcare investment and technological advancements have led to a surge life sciences growth across the nation. These two trends have set the stage for an unconventional solution: converting office buildings into lab space.
The Market Appetite for Lab Conversions
We’re seeing this concept of office to lab conversions gain traction across the US, particularly in markets where life sciences hubs intersect with world-class hospitals and leading universities. Cities like Boston, Philadelphia, New York, San Diego, and the Research Triangle in North Carolina are all attractive locations for life sciences companies looking to cluster near top talent from these academic and healthcare institutions—and that cluster effect often means we’re looking for lab conversion opportunities in very specific neighborhoods.
New York, NY
What Makes a Building a Good Candidate?
Lab spaces have specialized needs, and not every office building is equipped to meet them. In my experience, only a select few office buildings have the right attributes for conversion. When evaluating whether a building is a viable candidate for lab use, we consider several factors, including:
- Structural load. To support heavy equipment and reduce vibrations throughout the structure, labs require a live load capacity of at least 125lbs per square foot. The typical office building is only built to support 50lbs per square foot.
- Ceiling heights. The ceiling height of most office buildings (usually between 11 and 12ft slab-to-slab) should be the minimum ceiling height for a lab space. To accommodate mechanical systems and equipment, 14ft slab-to-slab would be ideal.
- Loading bays. With trucks of materials, supplies, and samples coming in and out all day, labs require a lot of loading birth capacity. Some loading bays must also meet specific requirements to ensure the safe transport and delivery of any hazardous materials.
Each of these requirements are difficult to find in a traditional office tower. The most promising candidates are usually office buildings that were formerly manufacturing facilities.
Take Innolabs in Long Island City, for example. Originally a manufacturing facility, it checked all the boxes: structural strength, floorplate size, and location in an emerging life sciences district. Our team at Pavarini McGovern led the transformation, gutting the MEP systems and reengineering the vertical shafts to handle massive air intake and exhaust needs. The result was a dynamic, flexible facility tailored to the needs of cutting-edge biotech tenants.
We also completed an office-to-lab conversion at 325 Hudson in Manhattan. A former industrial building turned telecom hub, the 1920s-era building’s infrastructure was already well-suited for heavy mechanical loads. Our repositioning work focused on modernizing all MEP systems, reconfiguring interior layouts to support flexible lab spaces, and upgrading the loading dock to optimize logistics and material handling. Since completion, 325 Hudson has attracted leading life sciences companies to the area.
At Barnard College’s Vagelos Science Center, our role involved converting the 118,000sf Altschul Hall into a lab space and building a new 99,000sf addition. On top of completing the conversion, Pavarini McGovern’s challenge was to blend the existing 15-story, 1966-built concrete structure with the contemporary, steel-framed addition. Today, the Vagelos Science Center stands as a beacon of scientific excellence.
Structure Tone Boston’s work with a confidential client in Cambridge, Massachusetts is another great example of an office-to-lab transformation. We actually renovated 24,000sf of the client’s own administrative office space into lab space, including a cold room, microscope support rooms, and chemical storage.
Conversion vs. New Construction
Why go through the trouble of selecting an office building and converting it when you can just build new? These conversions often cost less than new construction—think $400 per square foot for a conversion compared to $575+ for new builds. These projects also move faster. Depending on the project requirements, a lab conversion can be delivered in as few as 20 months of construction, while ground-up laboratories require at least 30 months. Conversions are also inherently more sustainable—conserving embodied carbon and reducing construction waste.
The Road Ahead
About two years ago, office-to-lab conversions were the hot topic. Owners were eager to transform underperforming office buildings into high-rent lab space. Today, the market is more educated. Real estate professionals understand it’s about identifying the right building in the right location and pairing it with the right team. With a strong demand for state-of-the-art lab space, these conversions offer a smart path forward for our clients looking to expand in booming life sciences hubs.
(Pavarini McGovern)
(Pavarini McGovern)
(Structure Tone Boston)