Since Layton Construction started using prefabricated exterior enclosure panels, they have seen significant benefits, from time and cost to safety and quality.
Saving time, reinforcing safety. Traditionally, completing the exterior of a large commercial
building requires lots of scaffolding and manpower. The process could take months,
but now it can be completed in a matter of weeks. Not to mention with no scaffolding, safety risks are cut considerably.
Controlling quality. Another advantage is quality control, especially when there is room
to build the panels on-site. When this is possible, they are constructed on the ground with
a small crew who can meticulously complete
each level unlike they could on a scaffold. Layton fits the panels together via a C clamp ratchet
system and gaskets, which will last longer than caulked joints. In addition, clients can choose the finishes they want, which are applied with a veneer.
Working the plan. A challenge with prefab panels is the learning curve in preplanning.
The team needs to make sure tolerances are built in and that everyone understands those tolerances. For example, a hot climate can affect the response of steel as it’s welded. If that happens, the steel can be out of tolerance. This isn’t good for the panels, so in pre-planning, the team needs to take steps to make sure the steel stays within a specific tolerance.
“Everyone wants predictability,” says Steven Knowles, Layton construction manager. “Prefab panels are one way we can help with that.”
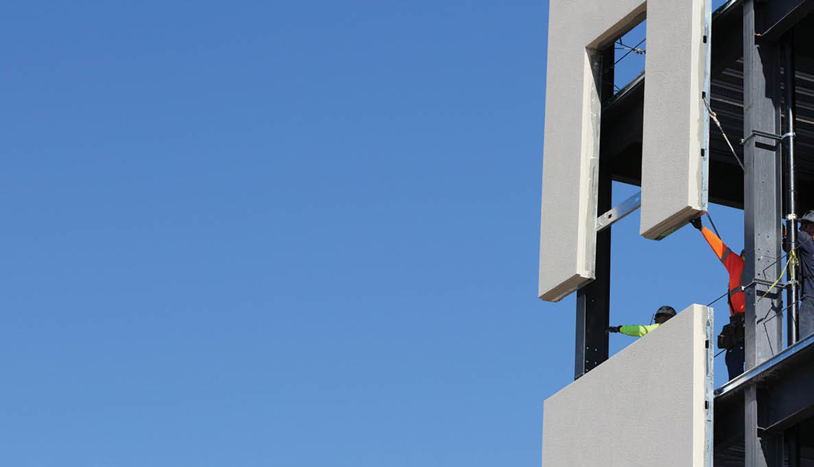