Mass timber is having a moment in both large and small construction. But it’s not a new phenomenon. In fact, cross-laminated timber, or CLT, traces its origins to advances in wood processing and fabrication about 30 years ago in Austria, Germany and Switzerland. Ten years later, the publication of Holzmassivbauweise (“solid wood construction”) provided the AEC industry with national guidelines for use of CLT in multistory buildings. The guidelines stimulated significant interest in countries with strong forest management histories, high-performance building energy standards and an emerging interest in reducing the carbon footprint of high embodied energy construction materials like concrete and steel. By removing and sequestering carbon from the atmosphere during growth, trees provide a vast renewable resource that reduces the carbon foot- print of buildings while simultaneously offering the opportunity to build faster by using prefabricated components and to deliver buildings that, in turn, use less energy to heat and cool.
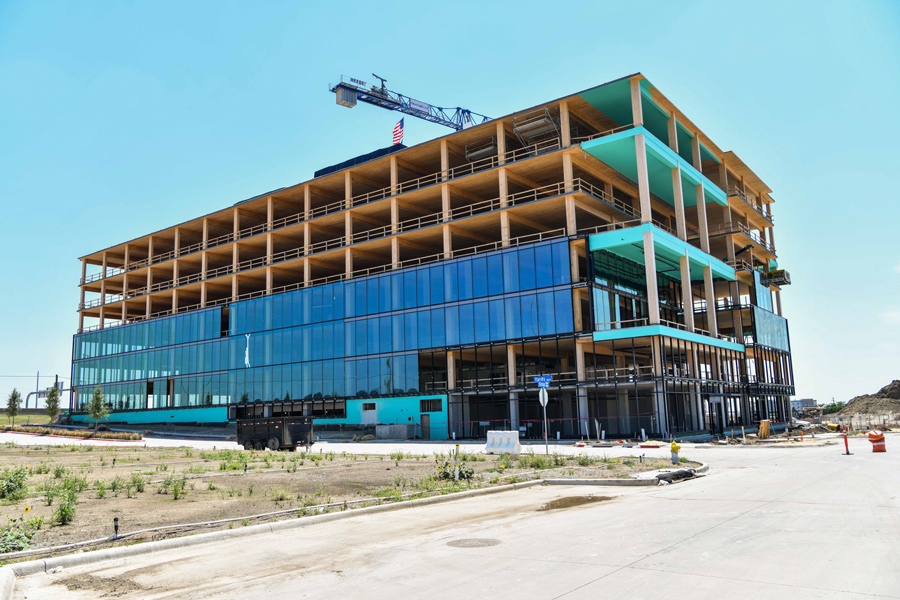
In the United States, the American Plywood Association (APA) published the APA PRG-320 Manufacturing Standard for Performance-Rated Cross- Laminated Timber in 2012. This, too, stimulated a dramatic uptake of CLT in commercial construction. Today there are five mass timber component manufacturers/fabricators in Canada and another seven in the U.S., with more to follow.
As the construction industry faces acute and worsening skilled labor short- ages, prefabrication and automated off- site construction offer numerous advantages, particularly to large building projects. Precision-controlled factory environments with technologically advanced processing and fabrication equipment deliver extremely precise mass timber components and can run three shifts if warranted. The factory Katerra built in Spokane, Wash., which has now been purchased by Mercer International, has the capacity to produce 6,475,000 ft of CLT per year, which equals 80 million board ft of lumber or 12 million sq ft of structural construction material. “If you apply those numbers to a typical six-story, 200,000-sq-ft, mass timber office,” says Pete Kobelt, the director of mass timber solutions for STO Building Group, “we could build 60 mass timber office buildings from that factory each year.”
Mass timber is also a potential tool in combating climate change. Harvesting and replanting smaller diameter timber resources reduces fuels and fire risk for our forests. As temperatures warm and droughts persist, the forests lose their innate ability to fight insects and become increasingly prone to catastrophic fire and the subsequent massive release of a carbon “bomb” back into the atmosphere. “Placing value on our forests as forests and protecting them from development affords us a vastly renewable resource while protecting clean air and water when done mindfully and sustainably,” Kobelt adds.
Innovations like mass timber design, engineering, manufacturing and construction across the AEC industries can be leveraged to meet emerging and increasingly urgent environmental goals. Most, if not all, of the major tech companies, automakers and corporations are making profound commitments to reducing their carbon foot- prints. They are looking for workplaces and facilities that help get them there.
Take, for example, Southstone Yards, a new office complex Structure Tone Southwest is building in Frisco, Texas, for Crow Holdings Development. The building combines a mass timber structural frame with a concrete core, forming a 238,000-sq-ft, seven-story structure integrated with an attached parking garage. Given the current demand for more mass timber construction, however, the team initially faced challenges in CLT manufacturing and procurement. “We were able to pivot quickly to find a second regional vendor in Alabama, which allowed us to remain on schedule and within budget,” says Chris Shackelford, STSW project executive. “As a result, Southstone Yards will open as the largest mass timber office building in the country.”
The building is also designed for LEED Silver, fitwel and WiredScore certifications, underscoring the owner’s commitment to creating spaces that meet the social and environmental standards that tenants are looking for. And meeting commitments like these is no small task. As Kobelt puts it, design and construction teams can offer alternatives like mass timber to help them deliver on these promises. “We can regrow this building in Texas’ vast Southern Pine forests in 150 minutes, or 9.6 buildings of this size every 24 hours. That’s the definition of renewable resources and sustainability.”