On a corner once occupied by a parking lot at Columbia University Irving Medical Center, something groundbreaking is rising—literally and figuratively. The Roy and Diana Vagelos Innovation Laboratories, Columbia’s newest biomedical research building, is being built to lead not only in science, but also in sustainability.
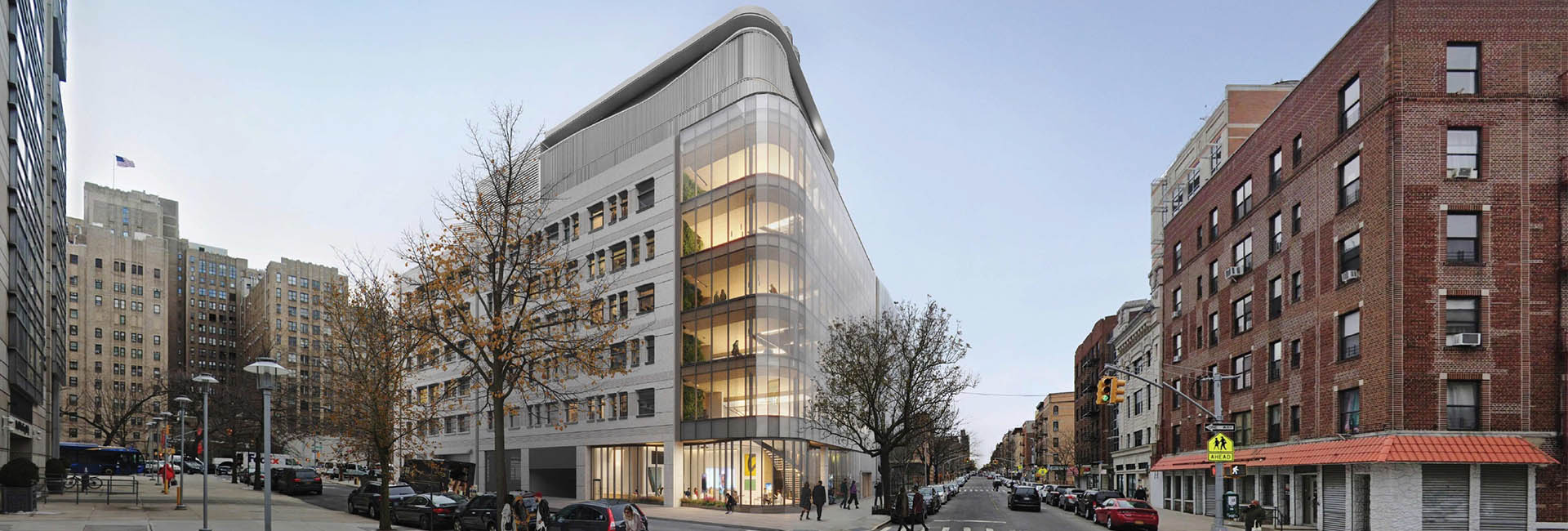
This facility will be the first purpose-built, all-electric academic research lab in New York City. It’s a bold statement—one that reflects both regulatory demands and institutional ambition. Designed to meet New York City’s Local Law 97 and to advance Columbia’s Plan 2030 climate goals, the new lab is set to redefine what research spaces can achieve.
Joseph Chin, LF Driscoll Healthcare’s senior vice president
for healthcare, says the project’s all-electric design marks a turning point.
Everything—heating, cooling, even hot water—is electric. “It’s more efficient
and will be the first of its kind to meet Local Law 97,” he says.
AN AMBITIOUS FOOTPRINT
This isn’t Columbia’s first foray into research facilities—but it may be its most complex. The new building is being constructed between two active sites: the Columbia School of Nursing and the Russ Berrie Medical Science Pavilion. These connections aren’t just symbolic. The new lab will physically link to both buildings, integrating into their existing infrastructure through carefully planned breakthroughs and shared spaces.
The building’s structure reflects this precision. The first six floors are concrete—unusual for research buildings of this kind, which are typically steel. The goal was alignment: concrete slabs allowed exact floor matching with neighboring structures. Above that, the structure transitions to a steel frame topped with metal decking and concrete. This hybrid approach not only makes the building more adaptable but also supports Columbia’s aesthetic goals—matching the concrete massing of one building on one side and glass finishes on the other.
NAVIGATING LOGISTICS
Construction hasn’t been simple. With researchers and students nearby, the team had to work with care—sometimes down to the decibel.
“There’s no work at night because it’s a residential neighborhood,” says Chin. “They are busy 24/7 because of the hospital, students, and neighbors. We have to work around that to make sure we’re not making too much noise.” To manage this, the team brought in a vibration monitoring firm, which placed 42 monitors throughout the adjacent buildings. Weekly coordination meetings with faculty and building staff help the team time their work around sensitive research, student activities, and major events like graduation.
And with the building fronting a public street and flanked by a garage that has to stay open throughout construction, site logistics are another challenge. Trade access, hoist placement, and pedestrian pathways has to been rethought and reconfigured several times. The even built a walkway over the sidewalk just to maintain hoist access.
INSIDE THE LAB OF THE FUTURE
Flexibility is a major theme of the project— not just in construction but in how the lab will be used. Floors two through six are being designed as wet labs, but with infrastructure that allows easy conversion to dry labs in the future. That flexibility was built into the design from day one.
Material sourcing also presented hurdles. With long lead times and rising global tariffs, the team prioritized early procurement. Curtainwall systems from Italy and lab equipment from Canada were ordered in advance to avoid potential delays and unexpected costs.
Building information modeling (BIM) and virtual design have been indispensable. “With this project, you’re dealing with tight ceiling heights and a massive amount of utilities—especially in a lab setting,” explains John Matist, senior superintendent at LF Driscoll. “Without VDC, managing the mechanical, electrical, and plumbing coordination would have been quite difficult.”
PROJECT DETAILS
Location: New York, NY
Size: 86,254sf
Client: Columbia University Medical Center
Architect: KPF
Engineers: AKF Group, a member of WSP (MEP); Hatfield Associates (structural); Langan (civil)
Certifications: Targeting LEED Gold
Sector: Life Sciences
Completion: Fall 2026
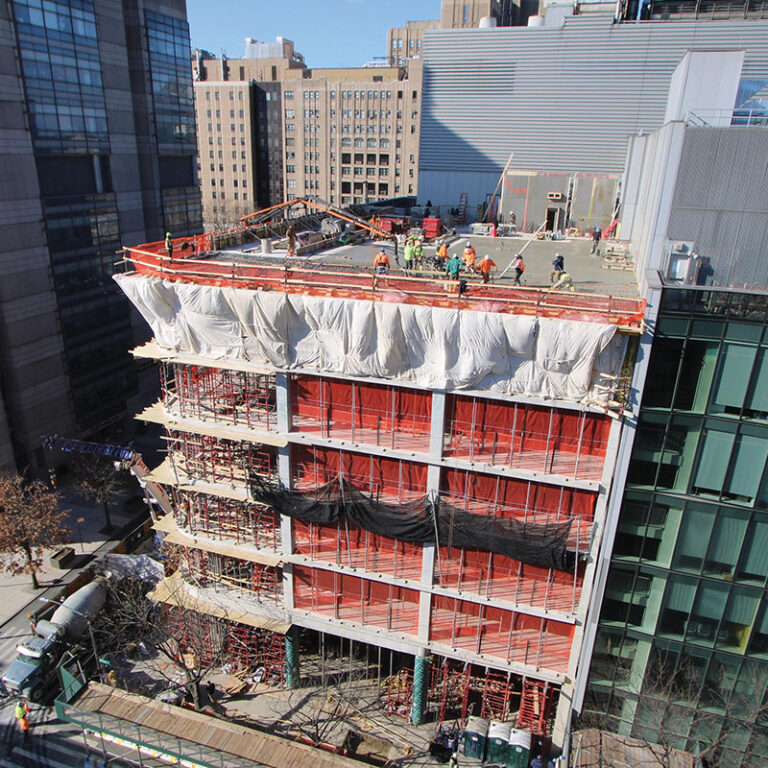
MOVING FORWARD, STAYING CONNECTED
Despite the obstacles, the project is progressing quickly. During the concrete phase, the team was completing a new floor every five to seven days. In April, they celebrated a topping-out milestone—a moment that underscored the collective effort behind the build.
“We have a lot of smart people on this jobsite who specialize in each portion—core and shell, façade, and lab work,” says James Bickerstaff, project manager at LF Driscoll. “Having those experts on-site really helped push the schedule and know what to look for.”
For Matist, the project’s significance goes beyond construction timelines. “We love that we’re building facilities that save people, find cures. It’s a great feeling.”
When complete, the Roy and Diana Vagelos Innovation Laboratories will be more than a state-of-the-art research space. It will be a landmark—a testament to what’s possible when science, sustainability, and collaboration come together.
.