For years, building contractors faced complaints of hand lacerations. The culprit? Metal studs. Despite warning labels and enforced PPE, the sharp edges of typical metal studs posed a sometimes-unnoticed threat, not only to workers but also to visitors to the jobsite.
In 2011, one regional manufacturing company created a drywall stud equipped with a rolled edge, which effectively reduced the risk of hand lacerations. Despite its safety benefits, this product faced challenges in gaining widespread adoption due to the need for nationwide availability and substitution approval from the design team every time it was specified for use. Keith Haselman, STO Building Group’s senior vice president of corporate safety, was determined to find a way to make studs like these standard and significantly decrease the risk of hand lacerations.
In 2017, Haselman got in touch with ClarkDietrich, the largest manufacturer of cold-formed steel framing in North America. Because ClarkDietrich supplied the majority of stud materials to the East Coast and has a nationwide presence, working with them to develop a new, safer product would make these studs standard to their process and their jobsite.
“My thought process was if they can make those edges safer as the largest manufacturer in the country, and we could get procurement to specify those studs, the safer product would become the preferred option and lead the market,” he says.
As an incentive, STO Building Group offered to specify deburred studs, or a rolled-edge substitution, during the procurement process to ensure safer material was being selected and supporting ClarkDietrich’s efforts. ClarkDietrich, in turn, also incentivized STOBG by ensuring there would be no additional costs.
Through a collaborative process involving samples and a few design iterations, Haselman and ClarkDietrich developed a “de-burred” product that was safe, functional, and met the approval of both parties. Once the product was approved for mass production, ClarkDietrich retooled their lines to ensure the final step in their manufacturing process included de-burring the edges.
“With feedback from customers and our commitment to safety, we developed Smart Edge™ technology. It is standard on our ProStud® Drywall Framing System, which rolled out nationwide with no extra cost,” says Jen Edgar, vice president of marketing at ClarkDietrich. “The result is an easier-to-handle product that reduces the risk of cuts and scrapes for installers, as well as for other trades who may come in contact with the framing.”
The launch of this product resulted in a flood of positive feedback from satisfied customers, and ClarkDietrich says it was validating to see their values lived out in such a collaborative process. “The overwhelming response has been ‘thank you for always doing the right thing,’” says Edgar. “From the roll form operator to the installer, we felt this was a win for them. We truly live our values, and one of them is ‘Do the right thing, do things right.’”
The implementation of this product brought significant benefits on-site as well. “Lacerations and hand injuries dropped by more than half,” reports Haselman.
And change doesn’t stop there. Haselman has continued to broach the subject and a safer alternative with other manufacturers. “It’s awesome to see our industry come together to solve challenges like these,” he says. “These partnerships are making a difference to reduce injuries and improve safety industrywide.”
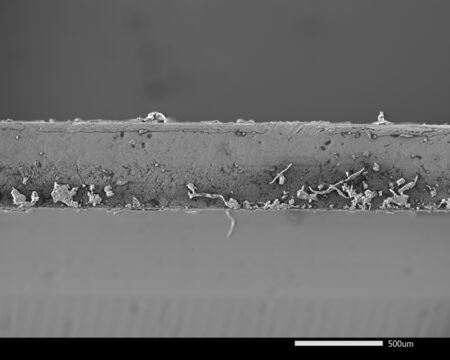
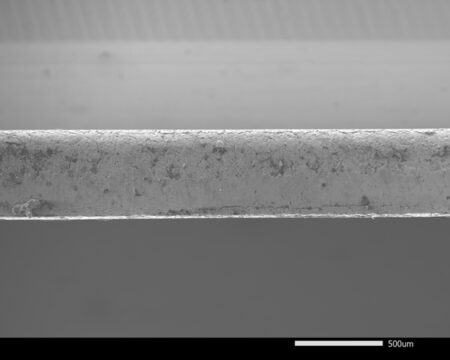