Built in 1914, the Lord & Taylor Building in Manhattan served as the retail giant’s flagship store for over a century and helped shape the city’s identity, including introducing Fifth Avenue as a premier shopping destination. In March 2020, Amazon purchased this landmark, transforming the department store (along with the neighboring Dreicer Building), into a modern, dynamic workplace for more than 2,000 employees. This new tech hub is known as “Hank.”
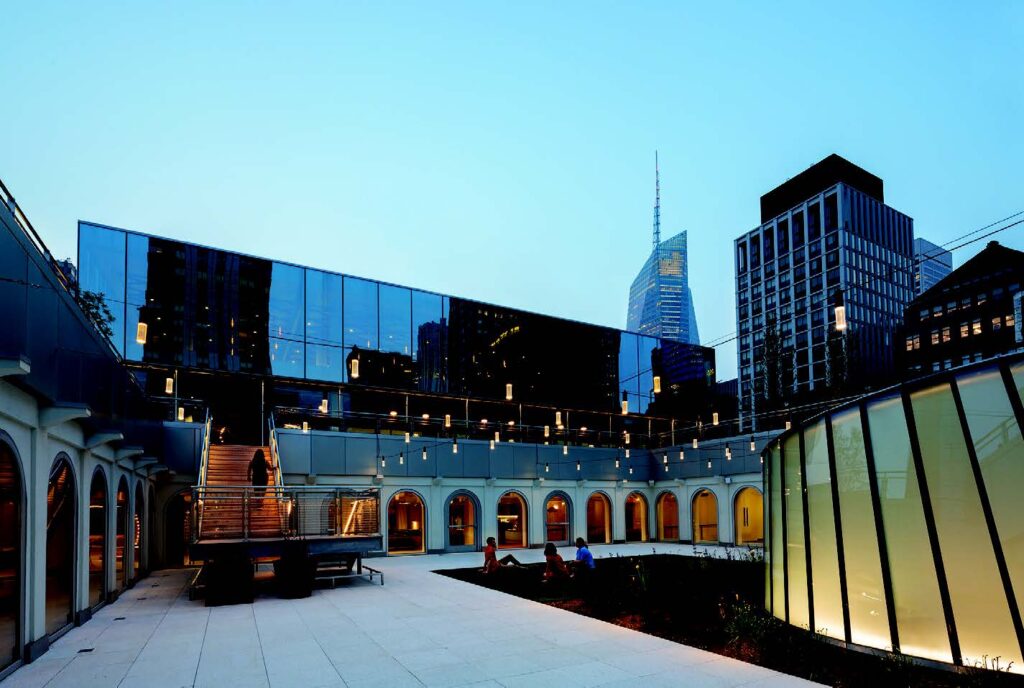
Working with the project team, Structure Tone managed the construction of this massive renovation project, turning the space into a cutting-edge office, combining the building’s architecture and historical elements with contemporary ideals of sustainability and wellness, while focusing on safety and schedule.
“This was an exciting project. Not only were we working for one of the largest companies in the world, but the scope had a bit of everything: interior fit-out, façade restoration, infrastructure upgrades, exterior terrace work,” explains Structure Tone senior project manager Josh Thompson. “The schedule was also super important; it was extremely fast-paced, with construction completed in just over 15 months.”
BUILDING AMAZON’S WORKPLACE
Following WRNS’ design, Structure Tone fit out 17 floors that include four interconnecting staircases, training rooms, meeting rooms, lounges, and conference areas with operable windows and configurable seats that promote comfort, space efficiency, and flexibility. There’s an expansive event space capable for up to 200 people on the top floor while an impressive terrace invites employees outside with a perimeter pathway and dog run. Inside, a spiral staircase makes it easy for employees to access the café, terrace, and courtyard.
The centerpiece of the project is an eight-story grand staircase that stretches from the second floor to the rooftop courtyard and connects the former department store to the neighboring Dreicer Building. With this staircase as the heart of the office, Structure Tone organized workspaces around the steps and arranged open desking near the perimeter for easy collaboration. The team also built public-facing training rooms, helping to advance Amazon’s commitment to the professional growth of its community and industry-academia partnerships. Various classroom spaces will be used by different local institutions, including the City University of New York (CUNY), for lectures and other academic events.
In addition to the interior fit-out, Structure Tone was responsible for a substantial infrastructure program. “We took over a good portion of the base building work that wasn’t initially in our scope,” describes Tom Patterson, account executive. “We checked out and commissioned the mechanical systems and made sure other systems were turned over properly without any extension of schedule.”
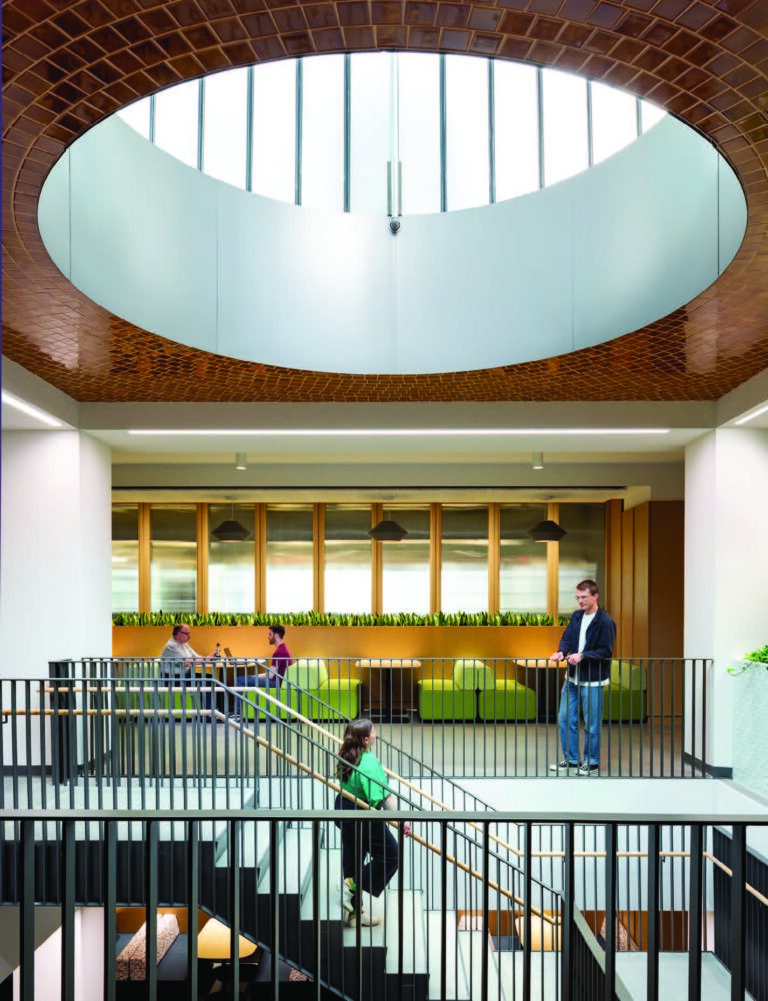
Additional aspects included the creation of two new skylights, including one atop the feature staircase, and the demolition and installation of the structural steel and concrete for four feature staircases, the longest of which ran 8 stories high and was fabricated in 16 pieces off-site. The team then lifted these pieces into the building via crane and trolley beams.
Structure Tone also managed the façade restoration, which required approval by the NYC Landmarks Preservation Commission. “We put up scaffolding on all four elevations and made detailed repairs to the building’s exterior,” recalls Thompson. “Restoring the decorative eagles was especially intricate, using a process that included gently removing each statue, using resin to create a mold, then pouring a replica using pins and rebar for reinforcement. The new ones look just like the originals from the early 1900s.”
Another significant improvement to the building’s infrastructure was the basement’s grout injection program. “There are four floors below grade, and because of the age of the building, these sub cellars would fill up with water with heavy or moderate amounts of rain,” Thompson says. “We drilled the perimeter walls and injected a grout-like urethane material that basically fills in the cracks and slowly stops water infiltration. Now Amazon has a dry basement, even when it rains.”
OLD IS NEW AGAIN: AMAZON’S COMMITMENT TO HISTORY SUSTAINABILITY
Prior to starting construction, the plan and design showed an intention to honor both the building’s fashionable roots and original design, while still providing a collaborative and sustainable workspace for Amazon employees. And that’s just the space the project team built. Well-preserved architectural elements were given new life: cast iron arches and glass windows now form an arched banquette; the new solarium features a restored skylight; and decorative terracotta in the ceilings and column capitals has been left exposed. Tiles from the former flower market now frame the signage for a restaurant that pays homage to Dorothy (Dot) Shaver, the first woman to lead a major retail company in the US. Wood panels imported from Scotland grace a new fireplace and brass lintels salvaged from old elevators create a sculpture. Selective new materials, colors, furniture, and fixtures also reflect the historic craftsmanship and incorporate current practices. The central staircase is capped by a transparent lantern, channeling natural light down to the lower floors and encouraging employees to move about different floors. This in turn supports Amazon’s goals for energy efficiency, minimized carbon, and employee wellness.
Updating a 110-year-old landmark isn’t without its challenges. The building is made of terracotta, which can be tough for installing advanced MEPS systems and architectural finishes: “sometimes, there’s good bearing for attachment, but other times, you have to try a couple times to find good anchor,” explains Patterson. Flooring also proved tricky, as the old substrate wasn’t consistently level. Structure Tone’s on-site staff put together extensive existing conditions reports and WRNS walked the site with the team weekly to confirm what was on the drawings, update the flooring if necessary, and ensure that construction proceeded according to schedule.
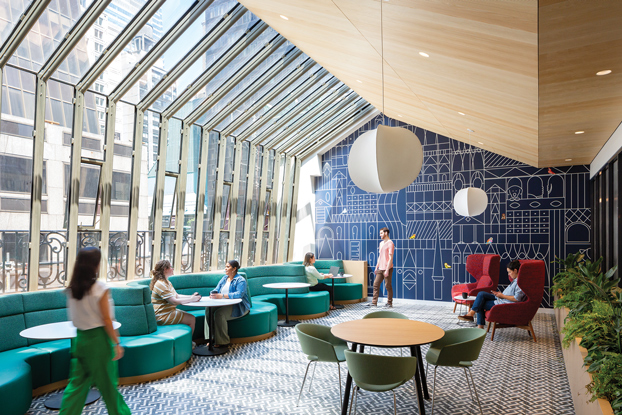
In terms of sustainability, the Structure Tone team was responsible for tracking embodied carbon and worker transportation emissions. Benchmarking environmental metrics is the first step before setting reduction targets. With goals like achieving net-zero carbon emissions by 2040, this tracking aligns with Amazon’s broader sustainability initiatives and demonstrates their commitment to reducing the carbon footprint associated with their buildings and operations. Benefits included:
Optimized Material Selection: By requesting as-built material quantities from subcontractors, the project team made informed decisions on material choices, emphasizing low-carbon alternatives.
Improved Supply Chain Efficiency: Understanding the embodied carbon within materials helped foster partnerships with suppliers focused on sustainable sourcing and led to a more efficient and environmentally conscious supply chain.
Data-Driven Decision Making: Data collected from tracking embodied carbon and emissions associated with worker commutes will inform future construction projects, enabling better decision making processes to further reduce environmental impacts.
In the end, the project team built Amazon a tech hub that utilizes and breathes new life into a historic piece of urban infrastructure. Thoughtful planning, imaginative interventions, efficient construction processes, and repurposing of materials cements the New York City landmark’s second act. Thompson agrees. “At first glance, it might seem unusual that Amazon wanted to take over an old department store. It’s remarkable how Amazon used the building’s history of retail and innovation as the vision for its NYC tech hub and inspiration for a new generation of employees.”
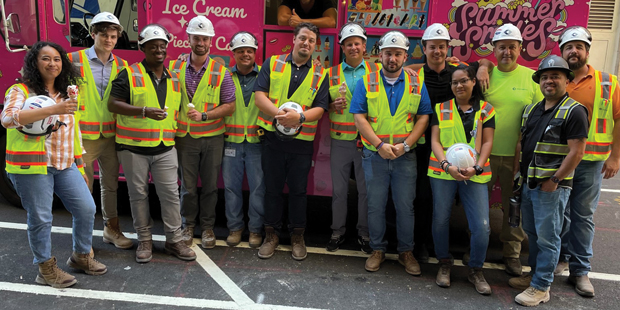