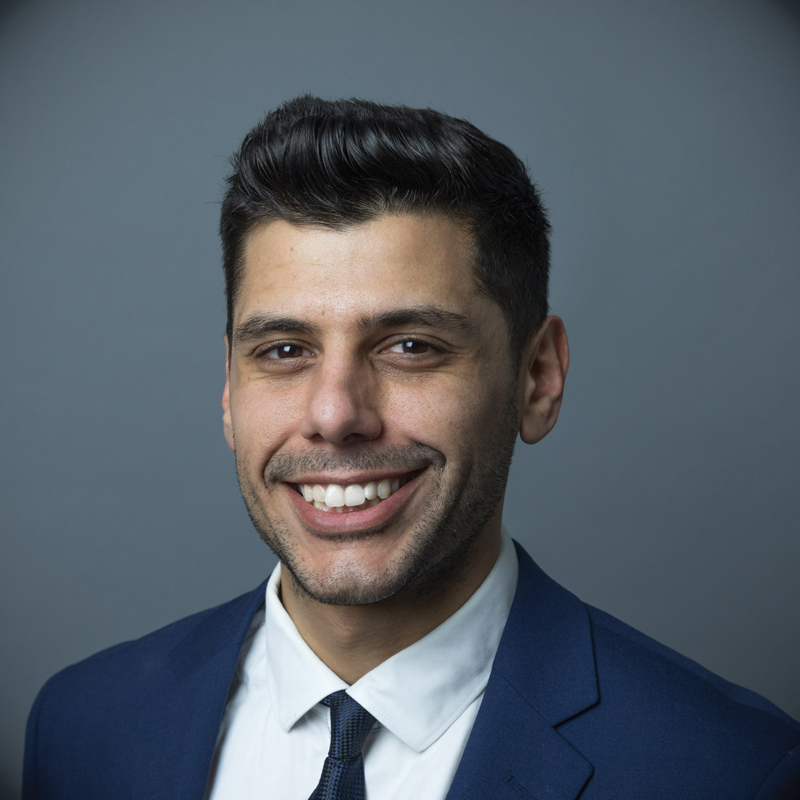
Written by Michael Signorile, Exterior Envelope Supervisor, Pavarini McGovern
As trends shift within the construction industry, one question is still in the forefront: How do we make our buildings efficient, sustainable, and cost neutral? For this reason, the Passive House Standard has become more prevalent within growing economic markets as well as larger cities pushing to meet demanding carbon reduction goals. Passive House construction significantly contributes to carbon reduction and aligns well with net-zero design ambitions in many ways.
WHAT IS PASSIVE HOUSE?
The Passive House Standard looks at achieving a rigorous level of energy efficiency while creating environmentally comfortable interior spaces. These principles can be applied to buildings of varying scales and types, from high-rise and mid-rise buildings, to retrofit applications, to a private home.
The Passive House Standard also looks at a building from a holistic approach to understand lifecycle and environmental impacts of building materials. This includes the extraction, manufacturing, transportation, use, and end-of-life phases. Implementing sustainable and low-impact materials can reduce the embodied carbon in the construction and contribute to a more environmentally friendly building.
For those unfamiliar with Passive House, the four primary principles of the Passive House Standard are:
- Thermal control: Building enclosure insulation, eliminating thermal bridges.
- Air control: Airtightness, balancing ventilation with heat and moisture recovery
- Solar radiation control: High-performance glazing, shading, and daylighting
- Moisture control: Vapor control, air humidity
These principles tie back into carbon reduction ambitions in many ways. Passive houses are designed to be extremely energy-efficient, minimizing the need for active heating and cooling systems. This results in significantly lower energy consumption compared to traditional buildings. Reduced energy demand directly translates to lower carbon emissions, especially when the energy used comes from conventional fossil fuels.
Passive houses feature a highly insulated building envelope, which helps maintain stable indoor temperatures. This reduces the constant need of mechanical heating and cooling systems, leading to lower energy consumption. New insulation products, as well as high-performing window and cladding systems, have entered the market to promote a decrease in the carbon footprint associated with the production and installation of the exterior envelope.
Air control helps minimize leakage in the building and the amount of energy needed to balance the heat lost through the leaks. The Passive House Standard promotes airtight construction and detail development early on in the design process. Airtight construction greatly reduces the need for oversized HVAC systems, further lowering the overall carbon impact associated with up-front equipment manufacturing, transport, and future operation.
This approach is based off the typology of the building. New construction has a significant difference in approach as compared to an existing building when designing and constructing a Passive House building. The key differences come from the challenges of existing conditions in retrofits versus the opportunities presented in new construction. Both approaches have very different impacts on the amounts of carbon reduction.
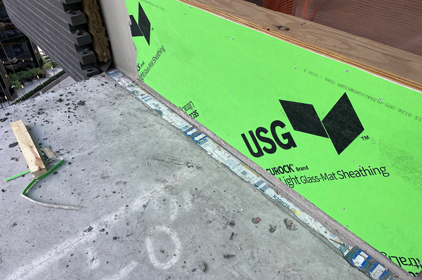
PASSIVE HOUSE APPLICATION WITHIN NEW CONSTRUCTION
In new construction, designers have greater flexibility to optimize the building’s layout, orientation, and envelope design to meet Passive House standards from the start. Essentially the client and design team are starting with a clean slate, limited by zoning, adjacent buildings, and also the regionalized climate. The design process, from the concept development through CD documentation, can integrate Passive House principles seamlessly without constraints imposed by existing structures (excluding adjacent buildings).
The building envelope can be designed and constructed to meet Passive House requirements without the need for significant alterations. The exterior envelope can be developed as per the design intent with the required amount of opaque wall area. There is a greater flexibility in the cladding design. A traditional design assist could take place for the wall, with greater confidence in the performance values being prepared. Windows can be strategically placed and sized to maximize natural light and solar gain while minimizing heat loss (if window wall or punched openings are utilized in lieu of a curtain wall). The aesthetic and expression become part of an overall design strategy rather than retrofitting existing openings. Achieving high levels of airtightness is easier in new construction, where the exterior wall can be designed with airtightness as a priority.
HVAC systems can be designed to meet the lower heating and cooling demands of the design, considering factors like energy recovery ventilation. Coordination and efficiency of running risers will always be much more cost effective in new construction as opposed to existing, where the risers may need to move or have more reinforcement provided where openings are made.
Quality control measures can be implemented throughout the construction process without the challenges of working with existing structures, resulting in potentially smoother implementation of Passive House principles. Preconstruction planning and phasing can be developed much earlier, without the need for probing, soft demo, and other prep that may be required for existing buildings.
Constructing a new building will always generate more carbon than an existing building due to the amount of materials needed for new construction. Constructing a new Passive House building involves producing and assembling new materials. While the building itself is designed for long-term energy efficiency and low operational carbon, there is an upfront embodied carbon associated with manufacturing and transportation of new materials.
In new Passive House construction, the building can be designed from the ground up to meet Passive House standards. Structural elements can be optimized without constraints from existing conditions.
PASSIVE HOUSE RETROFITS WITHIN EXISTING BUILDINGS
The biggest difference in carbon reduction between a new construction Passive House building and a retrofit Passive House building pertains to the extent of modifications required and the associated embodied carbon. There may still be embodied carbon from the production of additional materials and components needed for the retrofit. Retrofits should typically begin with an assessment of the existing building’s condition, including structural elements, insulation levels, age of the windows, age/efficiency of the mechanical systems and the feasibility of incorporating Passive House measures. Retrofit projects often require a delicate balance between achieving Passive House performance standards and preserving the historical or architectural integrity of existing structures.
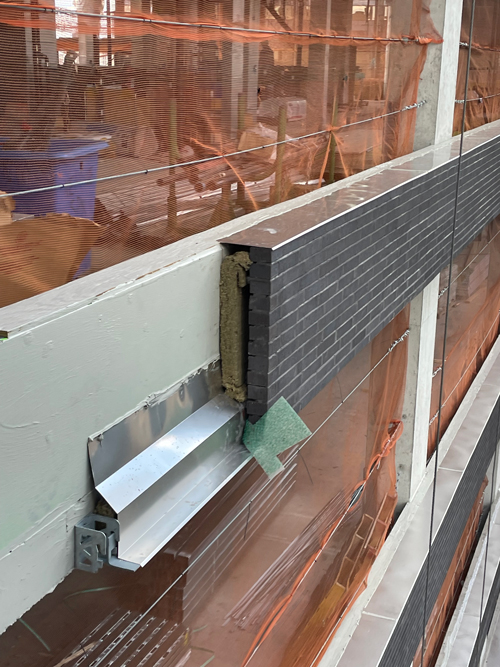
Retrofitting an existing building may require structural modifications to accommodate increased insulation or changes to the exterior facade. These modifications can contribute to additional embodied carbon and may vary in complexity. Usually within retrofit applications, there are generally three approaches to enhancing the exterior envelope:
- Overclad. This approach consists of cladding over the existing façade. This is typically performed on masonry facades, where a new vapor barrier is installed onto the masonry, followed by insulation and cladding. This approach is usually applied with EIFs. The main concern with this approach is the lack of maintenance/access to the backup wall once the overclad is installed; however, this is the most cost-effective approach.
- Re-clad. which consists of removing the existing façade to the backup wall. A new vapor barrier could be installed, followed by insulation and a cladding panel. This approach is beneficial since it gives the client and design team more flexibility on the visual aesthetic. The main concern with this approach is modifications and new supports potentially required within the structure to support the façade. There is a moderate cost to doing this option.
- Interior insulation. This approach insulates the façade from the interior side of the wall. There are challenges with insulating from the interior due to required level of airtightness due to existing openings, complex geometries, wall build-ups and potential air leakage points. Extreme care needs to be taken with this approach, but the wall itself on the interior is normally just a furring wall. This approach has the potential to be the least costly; however, this is dictated based on what is needed on the exterior of the building, whether recladding is being performed, or the façade is remaining as is. Also, one con to this option is the reduction of interior floor area due to the build-up of the wall.
Retrofit projects usually upgrade the entire MEP systems, which may require modifications or upgrades. Compatibility and retrofitting older systems can pose challenges and potentially contribute to embodied carbon. There could also be added cost due to increased structural supports at new shafts.
Quality control measures are very difficult with an existing building due to all of the concealed conditions that may appear. Preplanning is critical prior to release of materials, and this pre-planning should consist of constructability reviews, probe assessment, and review of the existing structure/materials the building is made up of.
PASSIVE HOUSE: THE CONTRACTOR’S ROLE
Passive House principles can be applied to both existing buildings and designing new construction. The main objectives of a Passive House are dictated by achieving a high level of energy efficiency and comfort. When assessing the lifecycle analysis and projected cost over time, it is important to understand how the construction approach impacts this analysis. Bringing on a qualified construction manager during the preconstruction phase helps streamline this process. Having a construction partner on the project team who understands these nuances and the effect they have on the process is critical to leveraging the efficiencies of the Passive House standard on our built environment. Whether new construction or a renovation, the decision to apply these principles should not be weighed against the aspiration of solely having a carbon reducing product or complying with the Passive House Standard. The decision between the two approaches depends on the specific context, goals, feasibility of adapting an existing structure, and constraints of each project.