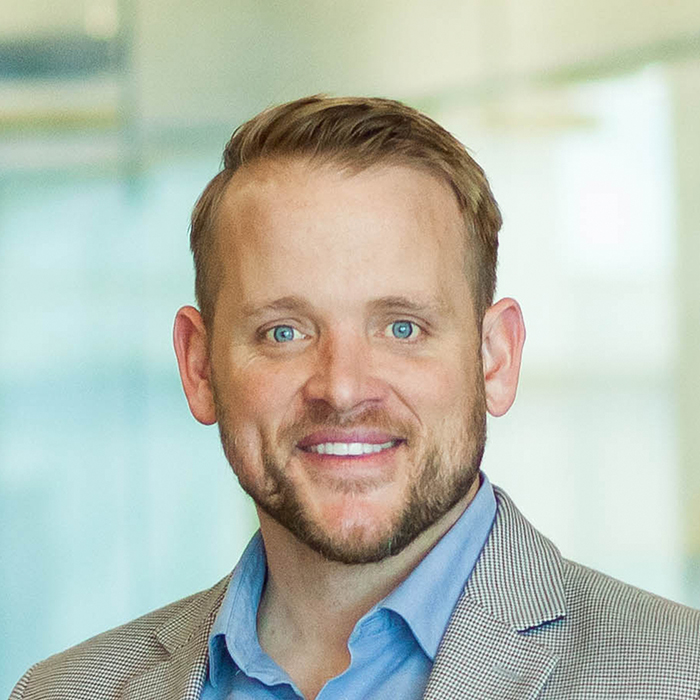
The last few years have been tough for the construction industry, dealing with challenges in the labor market, high interest rates and energy price volatility. Despite these challenges, however, government funding into the advanced tech market drives a strong industrial market in the Southeast.
With its close proximity to the ports, Eric Nay, Executive Vice President, National Building Group, Layton Construction Co., points out that the Southeast region has always been a strong industrial area and still seems to be fairly strong. “The Southeast is still an attractive market due to workforce available and the attractive labor costs and business-friendly tax environments for the business owners,” he says. “We still see the Southeast as a busy and active market.”
The American Institute of Architects (AIA) predicted in its 2024 AIA Consensus Construction Forecast that spending on nonresidential buildings would see a modest 4% increase after an increase of more than 20% last year, and that manufacturing construction would increase almost 10% this year before stabilizing in 2025. This comes after a very strong performance for the building sector in 2023, with manufacturing construction accounting for almost 30% of overall spending on nonresidential buildings last year.
This coincides with the Dodge Construction Network (DCN) Outlook 2024, which notes that manufacturing construction starts are expected to continue to grow with the onshoring of production, which will improve supply chains as well as the increase in federal funding. Starts are expected to outperform most other sectors with a 16% increase in dollar value and a 10% gain in square footage.
GOVERNMENT FUNDING
Aiding this growth is the Creating Helpful Incentives to Produce Semiconductors and Science Act (CHIPS Act), which favors onshoring and improvements to facilities in the semiconductor industry. Also helping is the Inflation Reduction Act, which provides funding to improve supply chains and bolster investment in domestic manufacturing. Between the two, billions of dollars have been poured into assisting manufacturers in building new facilities within the United States. Since 2020, DCN notes that starts have grown from 63 million square feet to more than 156 million in 2023, with continued growth expected this year.
“Our clients are still bullish, but are being more cautious on the deals they put together,” Nay notes. “Government funding from the CHIPS Act and the Inflation Reduction Act have continued to help fund the advanced tech sector and we see those as the largest portion of tenants and end users in the Southeast.”
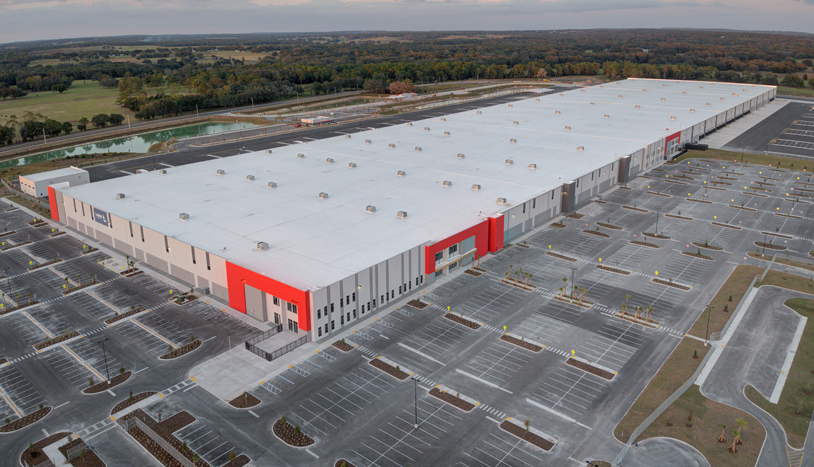
ADVANCED TECH LEADS THE WAY
According to Nay, the advanced tech sector is a major influencer on the industrial market, both from the tenant perspective and how it impacts facility design. “A big driver of the industrial growth in the Southeast is the amount of advanced tech companies building new facilities to support the supply chain in the EV and solar industries,” he says. “Often, these facilities have substantial power requirements, and they are looking at alternative energy or incentives with the power companies to source the power they need. Automation is constantly improving operational efficiencies, which can impact bay spacing and clear heights, which can impact what is considered industry standard.”
As the demand for advanced tech projects continues to grow, it’s overtaking the demand for large warehouses or big bombers. “We are seeing more of the smaller rear load or infill projects, as there is a bigger demand for the smaller leases,” he explains.
Additionally, Nay says there continues to be strong demand for build-to-suit projects, including those for cold storage and industrial manufacturing for automotive, solar, battery, etc. “Once the existing product gets leased up and when interest rates start to fall, we could see the spec market slowly start to come back, but we don’t know if it will be as hot as it has been the last several years,” Nay adds.
THE LABOR MARKET
The Southeast region has a reputation for being a more affordable market—a key reason it is a hotspot for the industrial sector. “Large data center campuses and semi-conductor facilities require a lot of labor, and we are seeing this impact some of the critical trades like mechanical and electrical,” Nay explains. “As demand for the labor increases, eventually the supply of labor will be strained, and companies will have to compete in different ways to attract the labor, both on the construction side and on the facility side. This could be in wages, amenities, benefits, etc. We are already seeing businesses include additional facilities or areas within a facility, like health and legal clinics, day cares, restaurants and fitness centers, for employees to utilize,” Nay says. “If interest rates drop later this year like the economists are forecasting, there could be even more demand, which would likely result in costs increasing, but for now they seem to be stable.”