By Shaun Patchell, Engineering Specialist, LF Driscoll
The rise of mass timber usage on projects in the US Northeast is a trend that is here to stay due to the material’s ability to respond to the construction industry’s impact on climate change while satisfying designers’ appetite for biophilic building solutions. Like the specialized engineering expertise required to deliver custom wall systems, complex mass timber projects comprised of glulam, cross-laminated timber (CLT), etc. lend themselves to early-award, design-assist bid packages. We thought we would share some key lessons learned from our experience selecting a glulam partner early in the preconstruction phase.
SINGLE-SOURCE DELIVERY
There are varying levels of “single-source delivery” in the mass timber market. For example, you can choose a vertically integrated company that controls the product from managing forestry and harvesting through fabrication and on-site erection. Or, you have the option of choosing a company who controls design, fabrication, and installs the final product, but sources the “raw” mass timber elements from a glulam/CLT manufacturer. There are benefits and limitations for both procurement options. For our latest mass timber project, we partnered with Nordic Structures to bring a streamlined engineering and procurement solution that comes from a fully vertically integrated company. In these COVID days, having a cohesive team managing the design assist package made coordination in the digital environment a breeze. More importantly, teaming up with a mass timber partner who controls the raw material reduced our project’s exposure to fluctuating costs of fiber, which is a volatile commodity that is impacting several trades’ material costs and ability to provide even short term commitments in the competitive bid environment.
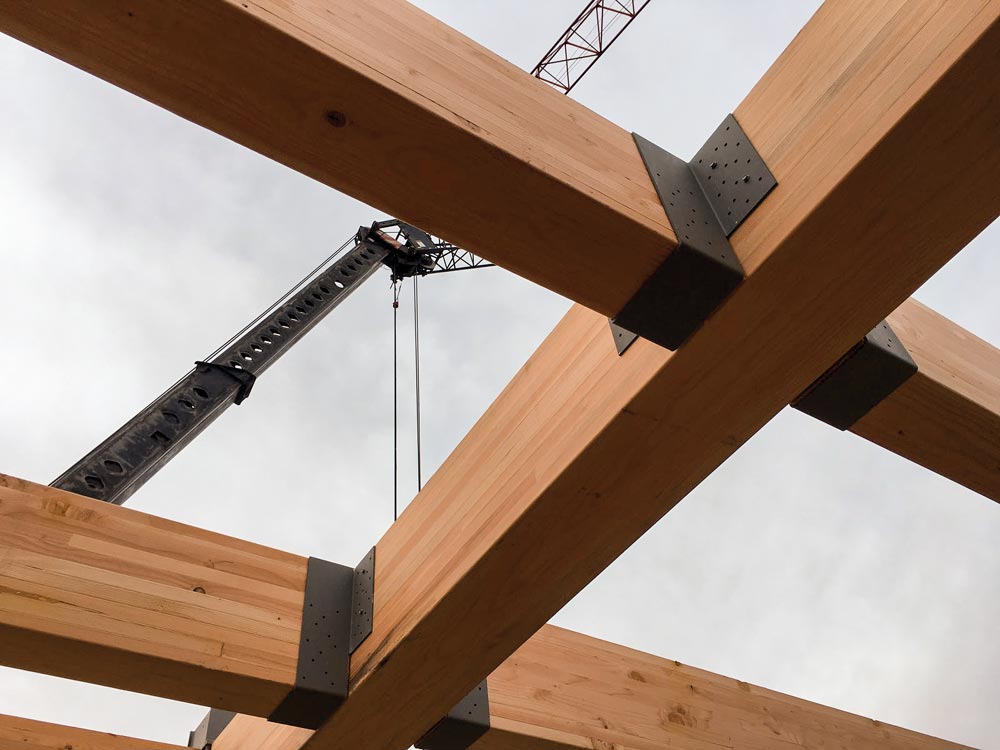
One limitation that came with our partnership with Nordic is that the design team was locked into a specific species of wood (Black Spruce) for its inherent aesthetic characteristics and engineering properties. Alternative subcontractors could source fiber from multiple manufacturers and, therefore, provide varying species but presented quality and cost control issues that come with a broken chain of custody. Different projects may warrant different directions in selecting the correct mass timber partner.
NORTH AMERICAN VS EUROPEAN VENDORS
Carbon footprint analysis was performed to compare the CO2 emissions associated with delivering glulam members from the Northwest and Northeast regions of North America and from Western Europe. Not surprisingly, domestic sources rely heavily on trucking which, from farther regions of North America, underperformed on emissions compared to cargo shipping from Europe. Using this information, we decided to entertain the use of European glulam vendors who offered similar delivery methods as described above. It should be noted that before European mass timber products are
considered, you should check the engineer-of-record’s willingness to accept EU testing standards in lieu of APA standards. If they are not willing to buy in to equivalency of engineering standards, use of European mass timber may be precluded.
BUILDING INFORMATION MODELING (BIM)
The erection tolerances for mass timber and integral steel connections are precise and rely heavily on computer-automated milling and CNC (Computer Numerical Control) fabrication. This level of automation brings the benefit of BIM into the early stages of design assist. Modeling efforts include locking
in on column and beam geometries, as well as coordination with MEP attachments/penetrations and steel attachment assemblies
SUSTAINABILITY BENEFITS
- Advancements in fabrication are allowing smaller sections of wood to be laminated, increasing the usable material within the tree structure and material efficiency as well as cost competitiveness. Manufacturers like Nordic Structures can use side cuts (known in sawmilling as “slash”) and small tree tips to yield up to 18% more viable fiber than traditional sawmilling.
- Wood manufacturing has the lowest embodied energy compared to concrete (represents nearly 10% of worldwide CO2 emissions annually) or steel (represents between 4–6% of worldwide CO2 emissions annually), and wood encapsulates carbon.
- Exposed mass timber elements contribute to the biophilic response in humans. Studies have shown reduced stress and heart rates in these environments, making them more attractive for commercial, academic, and residential projects.
- Each cubic meter of mass timber represents one ton of embodied CO2. It’s the only carbon-negative building material. And it grows free from solar energy, pulls CO2 out of the atmosphere, purifies water, and exhales oxygen.
CONSTRUCTABILITY BENEFITS
- At 1/5 the weight of an equivalent volume of concrete, wood not only allows for reductions in foundation structures, but also for more usable area in remediated and low-bearing soil conditions.
- Fabrication, delivery, and erection times are all reduced compared to steel and concrete structures due to material availability and precision of milling.
- Mass timber structures are secure for follow-on trades once there is a ceiling directly above, not several floors above as with steel deck or concrete shoring. Essential work can be completed by phasing in these trades much more quickly than in traditional concrete/steel projects.
- Mass timber fire-ratings are integral to the thickness of wood members, eliminating spray fireproofing inherent with steel construction.
- The resilience and light weight of wood make it ideal in seismic areas. Antiterrorist blast tests have also proven CLT structures to be more survivable than concrete and steel structures.