As the trend for more open, collaborative workplaces moves into the post-pandemic era, the feature staircase continues to add a “wow” factor to an office. But it’s also becoming more than a mere statement piece. Today, businesses use interconnecting steps as a unique design element to promote corporate culture, to encourage wellness, and to inspire collaboration and cooperation.
WHEN BUILDING A FEATURE STAIRCASE, REMEMBER S-T-A-I-R
Given the important role a feature stair plays in a finished workplace, building a signature staircase takes a certain level of expertise—and lots of planning —to get it right. Every staircase, no matter the size or scale, requires a tailored approach, from the schedule to the assembly to the finishes. The following lists out five critical elements to consider when taking on an approach to steps.
S is for Schedule. “Central staircases are usually the first thing to start and the last thing to finish,” says Jim Custodio, account executive in Structure Tone’s Boston office. From timing out ceiling work to tying the fire shutters into the fire alarm system, everything hinges on the progress of the stairs.
But there are always exceptions to the rule. During the build-out of a large corporate headquarters in one of downtown Boston’s newest high-rises, Structure Tone’s team proposed an atypical, out-of-sequence plan to help keep the project on track. “The building was far behind schedule in terms of the core and shell,” Custodio explains. “During preconstruction, we proposed to scan the floors and bid out the stair package almost immediately upon award. We figured if the design was finalized, why shouldn’t we get that work started right away? The client agreed and we got started. For the first time in my career, we completely installed the stair prior to starting construction. It saved the schedule quite a bit.”
T is for Trades/Procurement. As the schedule allows, taking advantage of the precoordination phase to review the staircase design in detail with the architect and ensure the proper trades and subcontractors are included in the schedule is crucial. Historically, there are multiple trades involved that require careful coordination. However, during a recent fit-out for a large financial company in Boston, Structure Tone’s team took a different approach, working with the subcontractor on the entire stair package, from the design-build to the millwork. This subcontractor came in early, scanned the floors, and created a model that could be shared with other trades. Building a model or mock-up of a portion of the stairs helps everyone—from the design team to the subcontractors to the client—see exactly how it all will come together, and what potential issues need to be addressed, all before the real staircase goes into fabrication.
A is for Access and Assembly. Building a massive staircase in an opening that spans several floors can get tricky. Do you start at the bottom and build up? At the top and move down? It all comes down to planning—mainly, access and assembly.
For a financial office fit out in Boston, the team designed the stair so that it came pre-assembled in large sections; everything—stringers, treads, risers—was welded together in the shop and then broken down into sections. The on-site project team then bolted the pieces together using a slip joint and used chain falls to raise it into the base structure. Custodio breaks it down more simply. “We had the company completely assemble it in their shop, break it down into four big pieces, make custom dollies for these heavy pieces, and then rolled them into the building for installation.”
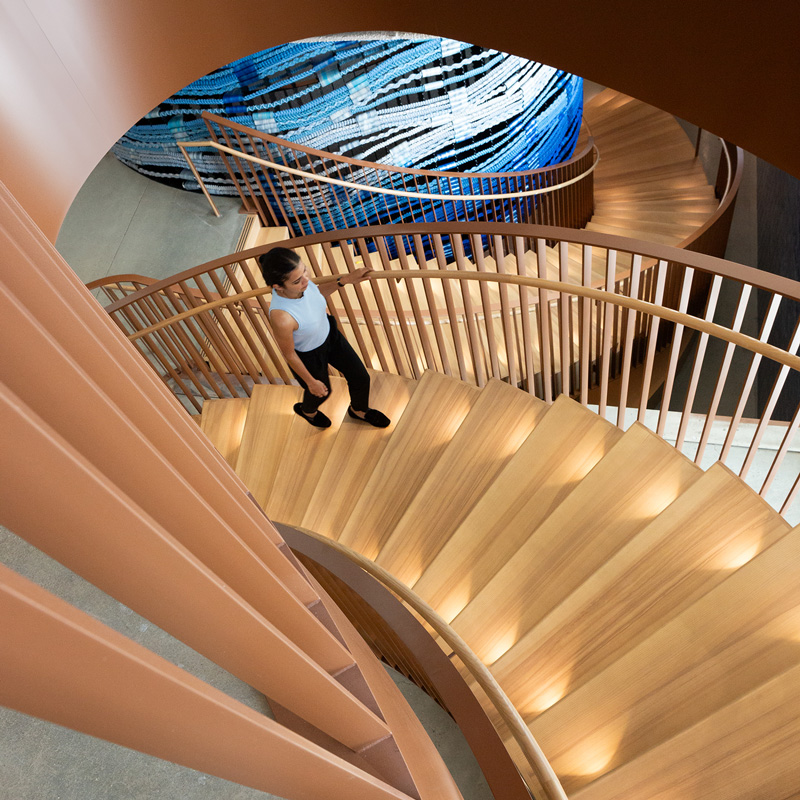
I is for Interior Finishes. Even the most meticulous designer can’t predict precisely how the finishes and materials of a staircase will align with each other, leaving a lot to the interpretation of the construction team. That makes coordination between the designers, contractor, and tradesmen critical. The designers can help the construction team make informed decisions on thickness of materials, angles, and other factors so that the transition is entirely seamless.
Structure Tone teams are also noticing an evolution in staircase trends and finishes. Transparent glass walls are being replaced with metal and mesh panels and intricate millwork. Custodio likens it to home kitchens, “You know how you can walk into a kitchen that’s 20 years old and tell exactly when it was built? Corporate stairs are going through a similar design cycle.” For example, his team is building a stair that features continuous millwork wrapping around both sides, emphasizing fine millwork details and how it links the openings together.
R is for Results. Every staircase truly does necessitate a unique approach. But designers, construction managers, and subcontractors can’t forget about the most important aspect of building a stair—the end result. What does the client want? While interconnecting staircases are certainly still the focal points of an office, they’re also being utilized in multiple other ways: as collaboration areas, for wellness, and to provide accessibility to other amenities. “Most of the stair installations I’ve managed recently have been built with cafés or fitness centers around them, says Custodio, “whereas years ago, I think the focus was more about coming into the reception area, seeing the stair combined with the view outside, and impressing both employees and visitors.”
And then there is final secret weapon—a project team. Building these kinds of staircases is complex, so engaging a team who has done it before is a huge advantage. Having a team that understands what goes into the process, the scheduling involved, and how to manage it all helps clients avoid complications and build the showstopper everyone envisions.