They’re featured in films, literature, and throughout pop culture…usually as a threat. But have no fear—robots are here to enhance our society rather than take it over. In the construction industry, robots can work alongside humans to help keep them safer and increase productivity. Here, Structure Tone Southwest operations manager Ryan Davis details their collaboration with Rugged Robotics, a Houston-based construction technology company, and the significance of robots on construction sites.
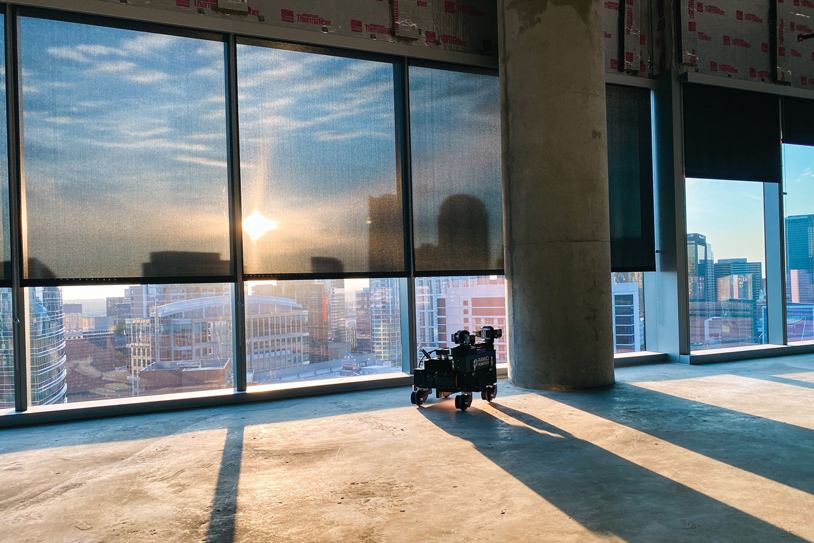
What is Rugged Robotics?
They are a robotics company focused on the construction process. Their primary product so far, a field layout robot, marks fully coordinated designs directly onto unfinished floors. We are using that tool on some of our projects in Texas.
Why did you want to try out on-site robotics?
The most significant challenges in today’s construction market are the shortage of experienced tradespeople, low productivity rates, and budgetary constraints. As we have seen in other industries, robotics may be the answer to mitigate these issues, as safety is one of the essential advantages of using robotics on project sites.
They aid in decreasing bodily injuries from heavy machinery, sharp objects, and machines that typically run at hot temperatures due to repetitive motion traditionally performed by manual labor.
How did you determine which direction to go?
Several robotics companies are looking to perform layout. Initially, I first came across a developer based in California that builds robot-powered tools for the modern construction workforce. When we were able to set up a meeting, they were not fully servicing the Texas area at the time—as well as other barriers such as having to train our staff to operate the new technology and only utilized fully coordinated BIM models, which on many jobs we do not have.
We also began coordinating with Rugged Robotics, a Houston-based company, who takes a different approach. They designed a robot to be fully self-sufficient and work from several different file types including the .CAD and . RVT files that we have access to on every project. Their team did the in-house programming to overlay the information from different sheets and then showed up on site to operate the robots.
What benefits have you seen so far?
Our Structure Tone Southwest team is currently working on the offices of a large investment bank, which was a challenging project to lay out manually due to the site conditions and model discrepancies.
The manual design of the space would have taken approximately two weeks. In contrast, the designated robot completed it in half the time, including the walls, headers, outlets, data, AV, and light fixtures.
What do you see in the future for robots in construction?
At Structure Tone Southwest, we plan to collaborate with Rugged Robotics to bridge the gap between common field challenges and the thought processes of the experienced teams to perform the layout generally. They have graciously taken these lessons learned and passed them on to their engineering staff. We were thrilled to have them back on our project sites to review the manual layout and see if they were able to solve any issues.